How to Screen Print T-Shirts at Home
Learning how to screen print a tee is easy. You can make something unique and turn any garment into a work of art. Just follow these 6 steps.
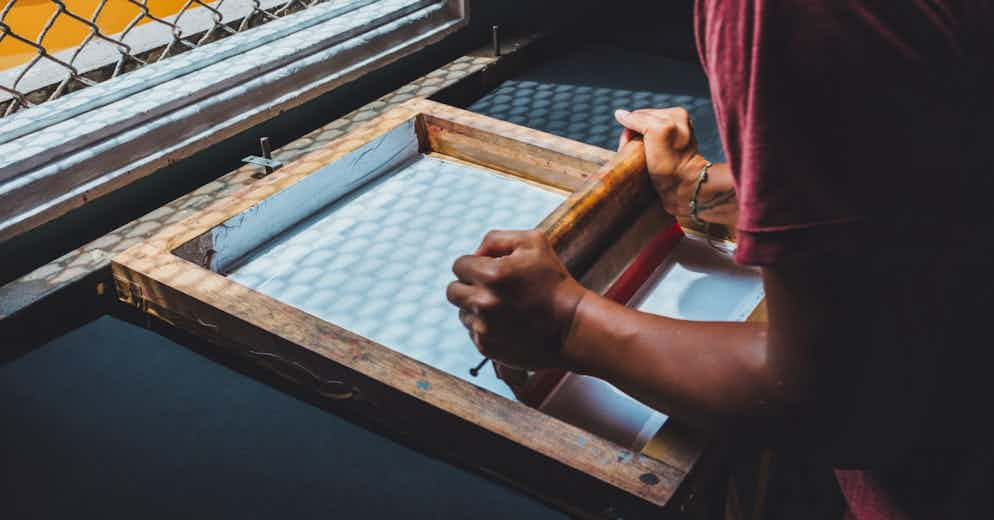
Screen printing is a fun and creative way to make custom t-shirts. You can print as many personalised tees as you want and you can upcycle what you already have in your wardrobe by adding new designs and colours.
If you want to start producing your own unique prints, whether to wear or to gift dad on Father’s Day, here we walk you through the entire process of screen printing from start to finish.
Start screen printing at home in 6 steps
Screen printing at home is easy. You don’t need expensive equipment or years of training to start printing your own t-shirts. Just follow these six steps and you’ll be on your way to making your first printed shirt in no time at all.
#1 Make sure you have everything you need
Before you do anything else, clear a space in your home that is large enough to accommodate a t-shirt screen printing station and all of your supplies and materials. You’ll need:
A blank shirt. You can print on cotton, rayon, or a blend of cotton polyester. You’ll also need some clean butchers paper for your test runs.
A silk screen. A silk screen frame is made of wood or aluminum with a fine polyester mesh stretched across it. Screens come in different sizes, depending on how big you want your design to be. You will tape your design in the form of stencil onto the silk screen.
Stencils. The easiest way to start designing is to prepare a papercut stencil. There are a variety of types of paper you can use. If you want your stencil to last, you can use plastic sheets or stencil paper, as long as your paper is smooth and does not buckle when wet.
Newsprint can be a great way to practice stencil cutting. When you become more experienced you may want to try photographic stencils. This method allows you to do highly detailed designs. It does take more equipment and experience but there are places where you can have your images put onto your screens.
A squeegee. This is a tool with a rubber blade on one end and a handle on the other. It is used to spread ink over your stencil and to push the ink through the mesh so that it can be transferred onto the t-shirt or garment you’re printing. Make sure to pick a squeegee that’s compatible with the type of ink that you plan to use.
Inks. There are many different types of ink for screen printing, but some of the most common are water-based, solvent-based, and plastisol inks. For beginners, it’s best to start off with water-based inks, which are safer and easier to use than other types of ink because they don’t contain toxic chemicals or require solvents to clean the screens. Water-based inks are ideal for cotton or polyester cotton mix fabrics or t-shirts.
Handy tools. There are a few tools and materials which you will need to complete the process:
- A stencil cutting knife or a craft knife for cutting out your stencil designs
- A cutting board which could be a recycled piece of cardboard
- A roll of packaging tape to tape stencils onto the screen and around the edges of your screen to stop ink bleeding out onto your shirt
- Spatulas for mixing inks, some clean containers for your own colour mixes, rags and rubber gloves for cleaning up
- A hair dryer for drying your design between colours
- An iron for heat setting your t-shirt after your print is completely dry
- You also need a pile of newsprint to put inside your t-shirt to stop ink going through to the back of the shirt.
Print space. You need to prepare a print space large enough to fit the fabric or t-shirt you would like to print. Find an old smooth blanket and some old sheets and create a print bed by putting the blanket on the table covered by the sheets. You might be able to source these from your local op shop if you don’t have anything you can use at home.
If you head to your local crafts store, you’ll find affordable all-in-one packs like “screen printing starter kit” with all the things you need to get started. For more advanced materials, try searching on websites that specialise in screen printing supplies.
#2 Sketch your design
So what would you like to print on your first shirt? If you’ve never made a stencil or done any kind of printing before, experienced textile print designer and teacher Julia Raath – owner of Surfaced and one of the amazing creatives behind Sunshine Print Artspace in Melbourne – recommends making some sketches on paper first:
“Sketching a design will help you get an idea of what you want to print. You then need to break the image down into areas of open space which you will cut out to create your stencil. Strong simple graphic designs can work very effectively as paper cuts but it is also possible to create intricate fine patterns.”
If you are inclined to do photographic stencils, Julia recommends using programs like Photoshop or Illustrator to create your stencils, by converting your own drawings, paintings, and even photographs.
“Working in black on white paper is a very easy way to start. I tend to do this when I start a design collection. Sometimes, it can start out as a little sketch using black pen on the back of an envelope as a doodle that then becomes a collection of screen prints.”
#3 Transfer your design to a stencil
Once you have an idea of what you’re going to be printing, use transfer paper (or carbon paper) and transfer your design onto your stencil paper. There are a number of different ways to do this depending on the complexity of the design and what medium you’re using, like a pencil, pen, Sharpie, paintbrush, and so on.
For pencil drawings, for example, to transfer it onto your stencil material, place greaseproof paper on top of your drawing and tape it down with masking tape or painter’s tape so that it stays in place. Then, with a pencil, trace around each element in order from left to right.
You can also draw directly onto your stencil material, if that’s easier for you.
If you have a multicoloured design you will need a stencil for each colour. You’ll most likely have multiple screens: one for each color or shade that will be printed on your shirt, so make sure each has its own unique design.
#4 Cut out your stencil
Once you have drawn your design onto the stencil paper you will need to cut out the areas in the design that you want the colour to print. Use either scissors or a craft knife to cut out your design. Just follow along the outside edge of where you just traced it in pencil. Don’t forget to use your cutting mat or sheet of cardboard under your stencil paper when you are cutting!
#5 Print a test run
Before you start printing your first shirt, use tape to secure the four corners of your stencil, making sure that your stencil covers all the open areas of mesh on your screen. If your stencil is rather small, cover the open areas with sheets of newsprint.
Next, take a plain piece of paper and do a test run using the same ink as you’ll be using on the shirt. This will help you see how well your stencils are working. Then, place the screen over the paper in the position where you want the design to appear.
Now, using your spatula, heap a few blobs of ink at the top end of the screen. Holding onto the side of the screen, take your squeegee in your other hand and use it to pull the ink through the mesh and stencil. Do three pulls of the squeegee to flood the screen and ensure you have good ink coverage. If anything looks off, fix it now so there are no surprises later.
Julia shares a couple of pro tips here:
- Watch out for bleeds. Make sure that the ink isn’t bleeding through the edges of your stencil. This can happen if you have overcut the edges of your shapes or if the paper you are using for your stencil is too absorbent, such that it bubbles up when the ink is pulled across the design. To fix this, place a test sheet onto your print table and push very hard with your squeegee across your design, which should flatten out the bubbled edges.
- **Check for smudging. **Smudging can happen for several reasons. For example, your screen can slip as you are printing, so you need to hold on to it firmly. Another way smudging can occur is when you are hanging your finished print to dry, and the colour goes where it’s not supposed to; so be very careful during this step and avoid it at all costs. But should it happen, you can try to remove the smudge by using a clean, damp sponge to remove the wet ink.
#6 You’re ready to screen print your shirt!
Printing on a shirt is a lot easier than you think. You can print on a t-shirt, a sweatshirt, a tank top, or even a hoodie. The most important thing is to make sure your shirt is the right size and shape.
First, put a sheet of newsprint inside your shirt and lay it flat on your print table. You should be able to see the design appear on your shirt as you pull ink through the holes. Next, take off the screen and move it over to another spot on your table, so that it doesn’t ruin any clean shirts by accident.
After you’ve printed the design on your shirt and it has completely dried, use a hot iron on a cotton setting and press it to heat set your print. Your tee is now ready to be worn and then washed later. Done!
Screen printing is a fun hobby that can also save you money. It’s much less expensive than buying screen-printed shirts from a designer or retailer, and it’s easy to learn how to do it yourself in your own home. From shirts, you can also use this technique on other things like pillows, mugs, posters, bags, hats, and more.
Got the perfect design in mind? Find a screen printing class near you and start creating your own custom t-shirts today!
Learn how to screen print your own t-shirts!
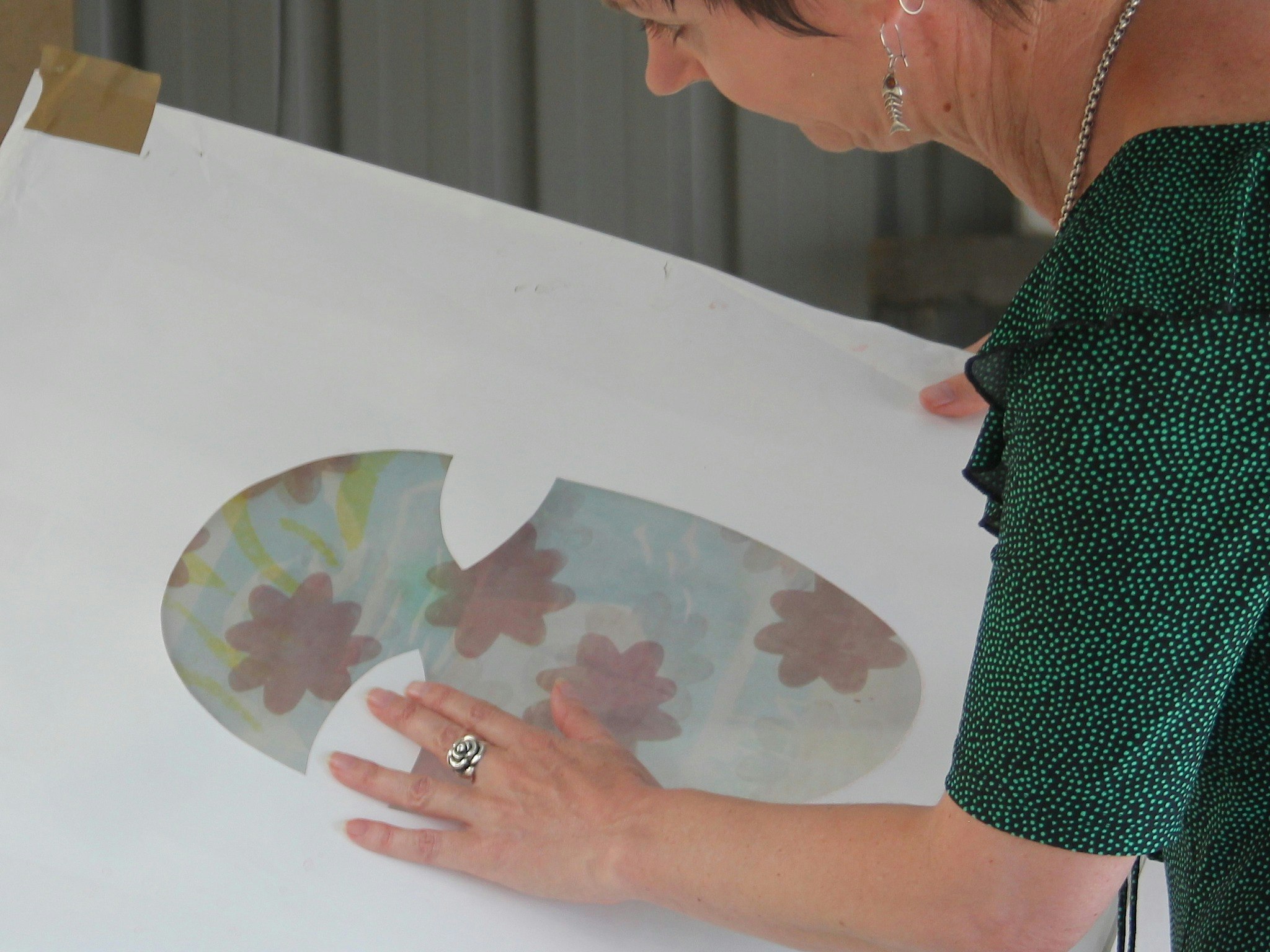
Introduction to Screen Printing
Create your own designs to screen print on fabric.